Tempra al laser per le cremagliere di precisione YYC distribuite da Romani Components
Romani Components, in continua e costante collaborazione con l’azienda taiwanse YYC, commercializza con successo cremagliere e relativi pignoni, temprati e rettificati. YYC si avvale di tecnologie all’avanguardia quali un impianto automatizzato per il trattamento termico al laser delle cremagliere standard.
La qualità di un’azienda la noti anche dai suoi investimenti. YYC, affermata azienda nella produzione di cremagliere di precisione, investe ogni anno una buona parte del proprio fatturato in ricerca e sviluppo per migliorare e incrementare i propri reparti e impianti produttivi.
Una delle più importanti innovazioni è stata proprio quella di sostituire la classica tempra induzione in passata, con una più efficace tempra laser dente a dente. Oltre a garantire la stessa durezza, questa tecnica evita eccessive deformazioni del pezzo che comporterebbero un oneroso e delicato processo di raddrizzatura.
In particolare, i sistemi laser destinati al trattamento termico superficiale dei componenti metallici destinati alla meccanica sono ritenuti antieconomici a causa di un elevato consumo d’energia, motivo per cui non hanno preso piede in tutte le aree di produzione.
I laser a diodi ad alta potenza, tuttavia, consentono di superare questo pregiudizio, poiché garantiscono un trattamento d’indurimento efficiente sia dal punto di vista energetico sia dal punto di vista di geometrie complesse dei componenti, offrendo, quindi, un’alternativa economica e interessante alla tempra a induzione.
Il trattamento termico è un metodo comunemente usato per aumentare la resistenza all’usura e alla fatica dei componenti in acciaio. In questo caso, per mezzo di una sorgente di calore, le zone prossime alla superficie del pezzo vengono riscaldate fino a un range compreso tra 900 e 1.500 °C, tanto che la struttura in acciaio, ferritica a temperatura ambiente, cambia in austenite.
Successivamente, si raffredda fino a temperature inferiori a 100 °C. Durante questo processo, gli atomi di carbonio vengono depositati in una struttura reticolare ad alta temperatura e non possono più diffondersi verso l’esterno a causa del rapido raffreddamento. Il risultato è martensite dura.
Un metodo consolidato è oggi il processo di tempra con raggio laser. Una volta applicazione di nicchia, oggi è impiegato con successo grazie alla sua alta precisione, in sostituzione di metodi di trattamento termico alternativi quali la tempra a induzione.
Gli input energetici locali troppo alti, durante la tempra a induzione, possono portare a una distorsione indesiderata del materiale, soprattutto nelle strutture con delle sezioni molto sottili. Tale deformazione può essere sistemata solo con un’ulteriore lavorazione da effettuare in seguito, la raddrizzatura.
Gli sviluppi della tecnologia, con l’avvento dei laser a diodi ad alta potenza, hanno permesso di superare gli ostacoli che spesso inducevano a scegliere la tecnica di tempra a induzione. I moderni laser a diodi ad alta potenza sono chiaramente superiori al laser a CO2: hanno la più alta efficienza delle prestazioni dei sistemi laser odierni, con un impatto significativo sui costi energetici; non solo, sono anche il tipo di laser oggi più favorevole in termini di costi di investimento.
Durante la tempra di pezzi identici, ad esempio, la tempra laser basata sul laser a diodi richiede, a seconda dell’applicazione, solo un decimo dell’energia di un processo di induzione. Uno dei motivi è l’elevato consumo di energia sproporzionato all’indurimento induttivo di geometrie complesse quando devono essere utilizzate le sezioni esterne della bobina meno efficienti.
Componenti come le cremagliere – con diverse aree adiacenti strettamente collegate e che devono essere temprate individualmente – non possono essere trattate con tempra a induzione a causa della loro geometria esigente. In questo caso, i sistemi laser hanno un chiaro vantaggio: il raggio laser insieme all’ottica di sagomatura del fascio focalizzabile con precisione consente un trattamento termico selettivo, in cui vengono elaborate solo aree selezionate dei componenti.
Con la combinazione di sistemi ottici di monitoraggio della temperatura come termocamere o pirometri con controllori di processo rapidi, l’apporto di calore può essere dosato in modo più preciso. Per questo motivo è possibile evitare temperature troppo basse, ma anche surriscaldamenti locali.
Rispetto alla tempra induttiva, vi sono ulteriori risparmi. A causa del riscaldamento rapido, dell’elaborazione selettiva e del controllo preciso della temperatura, il calore immesso dal raggio laser viene dissipato nel più breve tempo e senza mezzi di spegnimento aggiuntivi in altri strati di materiale (autoestinguenza). Non vi sono costi energetici aggiuntivi per il raffreddamento dei pezzi.
In conclusione, non si verifica nessuna distorsione del materiale e il processo di raddrizzatura risulterebbe un’operazione ridondante. La conseguenza? Una chiara riduzione del tempo di realizzazione delle cremagliere, che determina un enorme vantaggio in termini di costo e di consegna.
Sito Ufficiae Romani Components.
Fonte: www.tecnelab.it
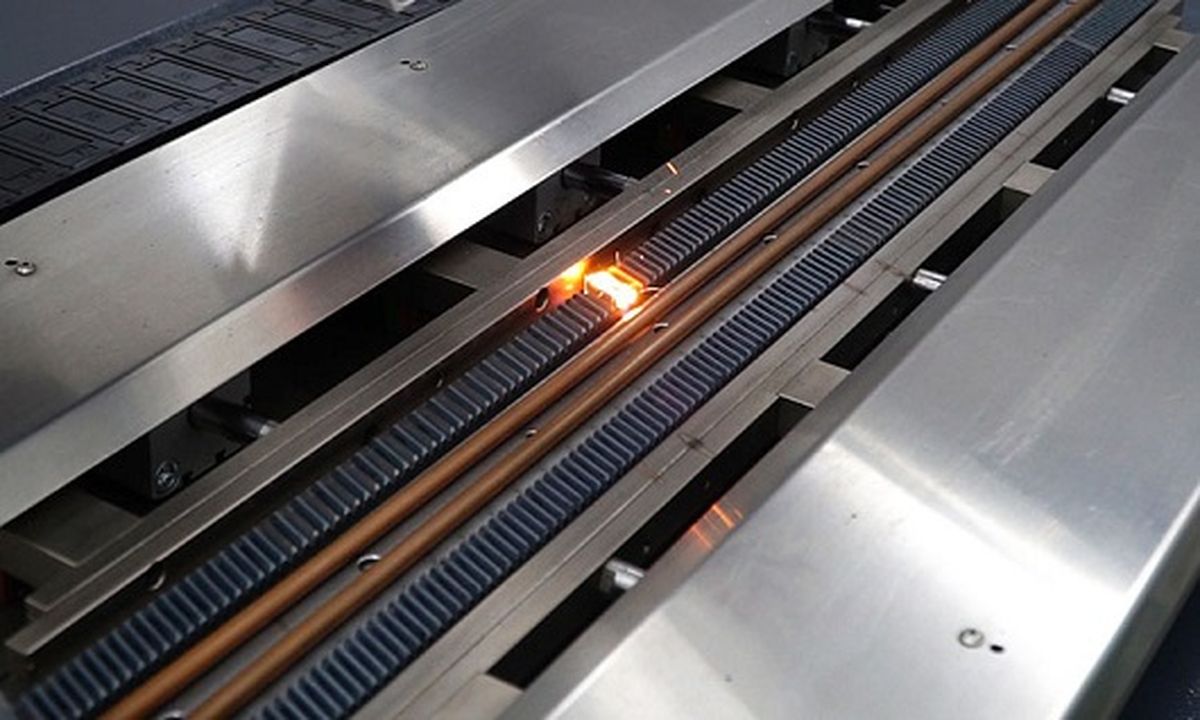